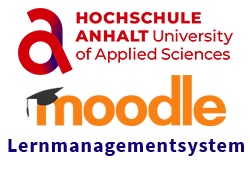
Login bei 'Moodle Hochschule Anhalt'
Neu auf dieser Webseite?
Authentifizierungsverfahren für Personal und Studierende der Hochschule Anhalt
Diese Lernplattform verwendet zur Authentifizierung das LDAP-System der Hochschule Anhalt. Verwenden Sie für Ihre Anmeldung Benutzername und Kennwort aus der zentralen Benutzerverwaltung der Hochschule Anhalt.
Externe Nutzer verwenden die Anmeldeinformationen, die sie vom E-Learning Service Moodle erhalten haben.